Jak Podłączyć Optymalizatory do Paneli Fotowoltaicznych w 2025: Praktyczny Poradnik Krok po Kroku
Zastanawiasz się jak podłączyć optymalizator do paneli fotowoltaicznych, by wydobyć z Twojej słonecznej inwestycji absolutne maksimum? Odpowiedź jest prostsza niż myślisz – optymalizator mocy montuje się szeregowo pomiędzy panelem fotowoltaicznym a inwerterem, niczym inteligentny łącznik przepływu energii. Wyobraź sobie niewielki, lecz niezwykle sprytny elektroniczny gadżet, który niczym osobisty trener dla każdego panelu, czuwa nad jego wydajnością, dbając o to, by nawet w najbardziej kapryśnych warunkach, cała instalacja pracowała na pełnych obrotach. To klucz do zdynamizowania efektywności fotowoltaiki, a poniższy artykuł rozwieje wszelkie Twoje wątpliwości!
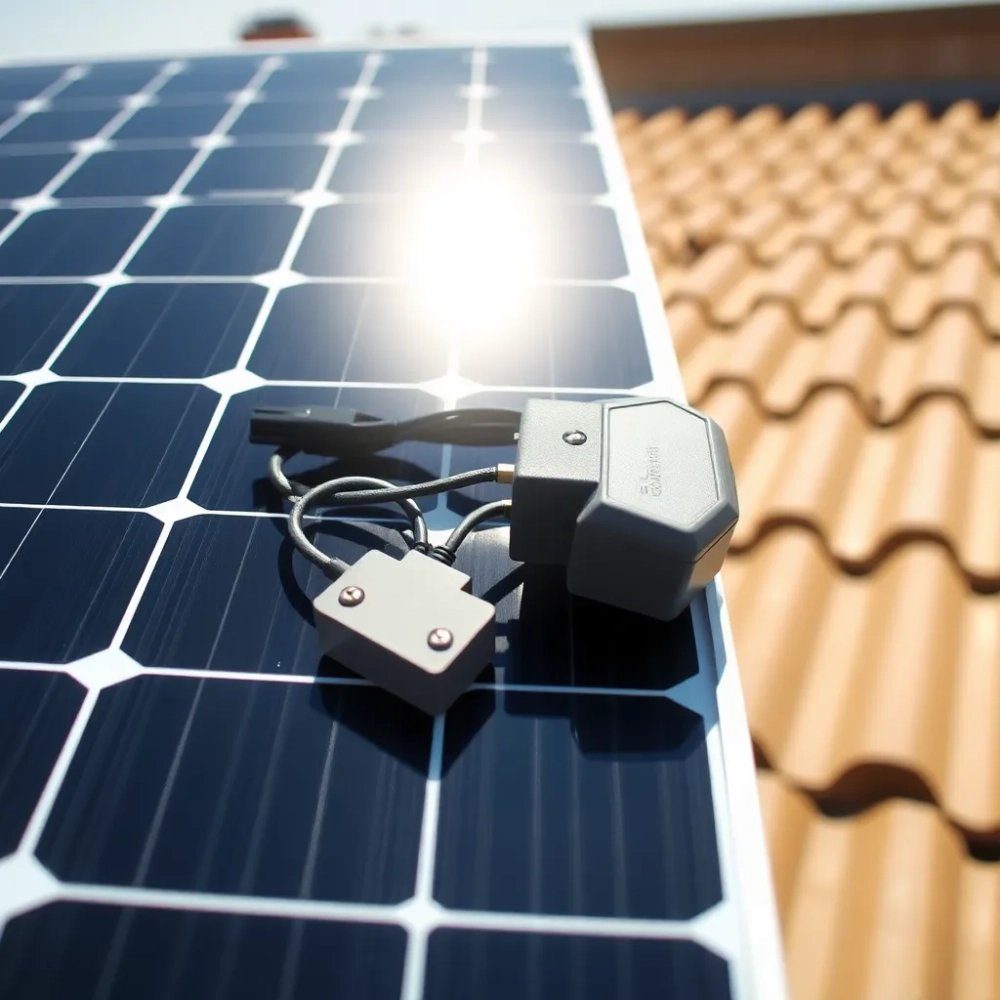
Analizując dostępne dane oraz doświadczenia instalatorów, da się zauważyć powtarzający się schemat korzyści płynących z zastosowania optymalizatorów mocy w systemach fotowoltaicznych. Chociaż bezpośrednie, jednoznaczne dane porównawcze są trudne do uzyskania ze względu na mnogość zmiennych (lokalizacja, rodzaj paneli, zacienienie, warunki atmosferyczne), pewne trendy wyłaniają się jasno.
Kategoria | Zastosowanie Optymalizatorów | Bez Optymalizatorów | Potencjalna Różnica/Korzyść |
---|---|---|---|
Wydajność systemu przy częściowym zacienieniu | Znacznie wyższa | Znacznie niższa, spadek mocy proporcjonalny do zacienienia, a często większy | Wzrost wydajności o 10-25% w warunkach zacienienia |
Produkcja energii w skali roku (lokalizacja z częstym zacienieniem) | Wyższa, bardziej stabilna | Fluktuacje produkcji, niższa średnia roczna produkcja | Roczne zwiększenie produkcji o 5-15% |
Monitorowanie i diagnostyka systemu | Szczegółowy monitoring każdego panelu, szybka identyfikacja problemów | Monitoring na poziomie stringu lub całego systemu, trudniejsza lokalizacja problemów | Lepsza diagnostyka i szybsza reakcja na awarie, minimalizacja przestojów |
Bezpieczeństwo instalacji (DC) | Możliwość zdalnego wyłączenia napięcia DC do bezpiecznego poziomu | Brak tej funkcji, wyższe ryzyko podczas prac serwisowych i w sytuacjach awaryjnych | Znaczące podniesienie bezpieczeństwa, szczególnie dla strażaków i serwisantów |
Koszty początkowe instalacji | Wyższe (koszt optymalizatorów) | Niższe | Wyższy koszt początkowy, kompensowany w dłuższej perspektywie przez wyższą produkcję i bezpieczeństwo. Przykładowy koszt optymalizatora na panel to ok. 200-400 PLN |
Zwrot z inwestycji (ROI) | Szybszy w lokalizacjach z zacienieniem lub złożonym dachem, porównywalny lub szybszy w innych przypadkach dzięki wydłużonej żywotności i optymalizacji produkcji | Potencjalnie dłuższy ROI w warunkach zacienienia, stabilny w idealnych warunkach nasłonecznienia. | Potencjalnie szybszy ROI, szczególnie w trudnych warunkach, dzięki wyższej produkcji i dłuższej żywotności komponentów. |
Przygotowanie do Instalacji Optymalizatorów: Kompatybilność i Niezbędne Narzędzia
Zanim przejdziesz do kluczowego etapu, czyli fizycznego połączenia optymalizatorów, fundamentem sukcesu jest staranne przygotowanie. To trochę jak z wyprawą w góry – bez odpowiedniego sprzętu i wiedzy, nawet najprostszy szlak może stać się wyzwaniem ponad siły. W przypadku instalacji fotowoltaicznej z optymalizatorami, ten „sprzęt” to kompatybilność komponentów i zestaw niezbędnych narzędzi.
Kompatybilność: Dobrany Zespół to Klucz do Sukcesu
Pierwszym i fundamentalnym krokiem jest upewnienie się, że wszystkie elementy układanki, czyli panele fotowoltaiczne, optymalizatory mocy i inwerter, mówią tym samym językiem. Kompatybilność nie jest tylko pustym hasłem marketingowym – to realna konieczność, porównywalna do dopasowania wtyczki do gniazdka. Wyobraź sobie próbę podłączenia europejskiego sprzętu do amerykańskiego gniazdka bez adaptera – fiasko gwarantowane. Podobnie, niekompatybilne komponenty fotowoltaiczne nie tylko nie zapewnią optymalnej pracy, ale w skrajnych przypadkach mogą doprowadzić do awarii systemu.
Zacznijmy od paneli. Optymalizatory są projektowane do współpracy z konkretnymi typami paneli – monokrystalicznymi, polikrystalicznymi czy cienkowarstwowymi. Kluczowe parametry to maksymalna moc panelu (Pmax), napięcie w punkcie mocy maksymalnej (Vmpp) oraz prąd w punkcie mocy maksymalnej (Impp). Informacje te znajdziesz w specyfikacji technicznej każdego panelu. Porównaj je z parametrami optymalizatora. Producenci optymalizatorów zazwyczaj udostępniają listy kompatybilnych paneli lub narzędzia online, które pomogą Ci w doborze. Pamiętaj, to nie jest czas na improwizację – tutaj precyzja jest królową. Przykładowo, optymalizator o maksymalnym prądzie wejściowym 10A nie będzie odpowiedni dla panelu generującego 12A w punkcie mocy maksymalnej.
Kolejny, nie mniej ważny element to inwerter. Optymalizatory mocy w większości przypadków współpracują z konkretnymi modelami inwerterów. Niektóre systemy wymagają dedykowanych inwerterów od tego samego producenta co optymalizatory, inne są bardziej uniwersalne, ale nadal wymagają certyfikacji kompatybilności. Ponownie, zajrzyj do specyfikacji – zarówno optymalizatora, jak i inwertera. Zwróć uwagę na protokoły komunikacyjne – czy inwerter wspiera protokół, którym komunikują się optymalizatory (np. Modbus TCP, SunSpec). Upewnij się, że inwerter jest zdolny do obsługi optymalizacji na poziomie modułów (Module Level Power Electronics – MLPE). Jeśli wybierasz optymalizatory z funkcją szybkiego wyłączania (Rapid Shutdown), sprawdź, czy inwerter jest z nią kompatybilny i posiada odpowiednie certyfikaty bezpieczeństwa (np. UL 1741 PVRSS w USA). Ignorowanie kompatybilności inwertera to jak próba uruchomienia najnowszego oprogramowania na starym komputerze – może i wystartuje, ale o płynnej i efektywnej pracy można zapomnieć.
Nie zapomnij również o kompatybilności elektrycznej całej instalacji. Sprawdź maksymalne napięcie systemu (Vsys) – suma napięć obwodów otwartych paneli (Voc) po uwzględnieniu współczynników temperaturowych, pomnożona przez odpowiedni współczynnik bezpieczeństwa, nie może przekroczyć dopuszczalnego napięcia optymalizatorów i inwertera. To jest szczególnie istotne w przypadku dużych instalacji z długimi łańcuchami paneli. Przykładowo, jeśli masz panele o Voc 40V i planujesz łańcuch 20 paneli, Voc stringu wyniesie 800V. Dodając współczynnik bezpieczeństwa, napięcie może przekroczyć 900V. Upewnij się, że wszystkie komponenty są certyfikowane na co najmniej 1000V lub 1500V, w zależności od wymagań norm. Błędy w doborze napięć to proszenie się o kłopoty – od ograniczenia wydajności po poważne awarie, włącznie z ryzykiem pożaru.
Niezbędne Narzędzia: Skrzynka Narzędziowa Instalatora PV
Posiadanie odpowiednich narzędzi to połowa sukcesu każdego fachowca, a instalator fotowoltaiki nie jest wyjątkiem. Do instalacji optymalizatorów nie potrzebujesz specjalistycznego sprzętu kosmicznego, ale kilka kluczowych narzędzi znacząco ułatwi i przyspieszy pracę, a przede wszystkim – zapewni bezpieczeństwo i poprawność wykonania. To trochę jak z gotowaniem – dobry kucharz potrzebuje ostrych noży i dobrze wyposażonej kuchni, aby stworzyć kulinarne arcydzieło. Ty, jako instalator, potrzebujesz solidnej „kuchni” narzędziowej, aby Twoja instalacja fotowoltaiczna była prawdziwym „dziełem sztuki” inżynierskiej.
Podstawą jest klucz dynamometryczny. Precyzyjne dokręcanie złączek i śrub jest kluczowe dla zapewnienia trwałego i bezpiecznego połączenia elektrycznego. Zbyt słabe dokręcenie to ryzyko poluzowania się złącza i wzrostu rezystancji, co prowadzi do przegrzewania i potencjalnego pożaru. Zbyt mocne dokręcenie to ryzyko uszkodzenia złącza lub izolacji. Klucz dynamometryczny z regulowanym momentem obrotowym to must-have. Zakres momentu obrotowego powinien być dostosowany do specyfikacji złączek MC4 lub innych używanych w instalacji (zwykle 2-3 Nm). Pamiętaj, „na oko” to nie jest metoda – moment obrotowy ma znaczenie. Inwestycja w porządny klucz dynamometryczny to inwestycja w bezpieczeństwo i trwałość instalacji. Dla przykładu, złącze MC4 źle dokręcone może powodować wzrost temperatury o kilkadziesiąt stopni Celsjusza, co w dłuższej perspektywie prowadzi do degradacji izolacji i problemów.
Zaciskarka do złączek MC4 to kolejne niezbędne narzędzie. Jeśli planujesz samodzielne zarabianie kabli, solidna zaciskarka jest absolutnie konieczna. Tanie, marketowe zaciskarki często nie zapewniają odpowiedniego zacisku, co skutkuje słabym kontaktem elektrycznym i problemami w przyszłości. Wybierz zaciskarkę renomowanego producenta, z wymiennymi matrycami, dostosowaną do różnych przekrojów kabli (zwykle 4mm² i 6mm² w instalacjach PV). Sprawdź, czy zaciskarka posiada mechanizm zapadkowy, który uniemożliwia otwarcie zacisku przed osiągnięciem odpowiedniego docisku. To gwarantuje powtarzalność i jakość każdego zacisku. Inwestycja w dobrą zaciskarkę szybko się zwraca – oszczędzasz czas, nerwy i unikasz problemów z połączeniami. Wyobraź sobie sytuację, w której instalacja działa z obniżoną wydajnością przez słabe złącze, a Ty musisz spędzić kilka godzin na szukanie i poprawianie wadliwego połączenia – to kosztowny i frustrujący scenariusz, którego można uniknąć dzięki porządnym narzędziom.
Oprócz tego, w Twojej skrzynce narzędziowej powinny znaleźć się przecinak do kabli, ściągacz izolacji, wkrętaki (krzyżakowy i płaski), imbusy, poziomica, miarka, multimetr, miernik cęgowy DC (do pomiaru prądu stałego) oraz tester ciągłości obwodu. Multimetr i miernik cęgowy to Twoi niezastąpieni sprzymierzeńcy w diagnostyce i weryfikacji poprawności połączeń. Sprawdzisz napięcia, prądy, rezystancję – wszystko, co niezbędne, aby upewnić się, że instalacja jest bezpieczna i działa prawidłowo. Tester ciągłości obwodu pomoże szybko zlokalizować ewentualne przerwy w obwodzie. Nie zapomnij o narzędziach do prac monterskich na dachu – klucze nasadowe, klucze oczkowe, młotek, wiertarka udarowa (jeśli montujesz konstrukcję na dachu). Bezpieczeństwo przede wszystkim! Kask ochronny, rękawice izolacyjne, pasy bezpieczeństwa (jeśli pracujesz na wysokości) to absolutne minimum. Praca na dachu to nie spacer po parku – zachowaj ostrożność i nie ryzykuj zdrowia dla oszczędności czasu.
Podsumowując, solidne przygotowanie do instalacji optymalizatorów to inwestycja, która procentuje na każdym etapie – od samego montażu, przez uruchomienie, po długoterminową eksploatację. Kompatybilność komponentów to podstawa, a odpowiednie narzędzia to klucz do sprawnego, bezpiecznego i trwałego wykonania. Nie bagatelizuj tych aspektów – to one decydują o sukcesie Twojej fotowoltaicznej misji.
Krok po Kroku: Fizyczne Podłączenie Optymalizatorów do Modułów PV
Mając za sobą etap przygotowań, nadszedł czas na działanie – fizyczne podłączenie optymalizatorów do modułów fotowoltaicznych. Ten etap, choć wydaje się być kulminacyjnym momentem instalacji, w rzeczywistości jest logiczną konsekwencją wcześniejszych kroków. To niczym układanie puzzli – mając wszystkie elementy pasujące do siebie i instrukcję, złożenie całości staje się przyjemnością, a nie frustrującą walką. Pamiętaj jednak, nawet przy najlepszych puzzlach, skupienie i precyzja są kluczowe, by obraz był kompletny i bez skazy.
Montaż Optymalizatora na Konstrukcji lub Ramie Panelu
Pierwszym krokiem w fizycznej instalacji optymalizatorów jest ich mechaniczne zamocowanie. Optymalizatory, pomimo swojej zaawansowanej elektroniki, są zazwyczaj kompaktowe i lekkie. Producenci przewidują różne metody montażu, aby dopasować się do różnorodności konstrukcji i ram paneli fotowoltaicznych. Najczęściej spotykane są dwa rozwiązania: montaż bezpośrednio do ramy panelu PV lub do konstrukcji wsporczej. Wybór metody zależy od typu optymalizatora, konstrukcji dachu i preferencji instalatora.
Montaż bezpośrednio do ramy panelu PV jest popularny ze względu na swoją prostotę i szybkość. Wiele optymalizatorów posiada specjalne klipsy montażowe lub śruby, które umożliwiają przymocowanie urządzenia do profilu ramy panelu. Ważne jest, aby upewnić się, że klipsy są odpowiednio dopasowane do grubości ramy i zapewniają pewny i trwały chwyt. Śruby należy dokręcać z odpowiednim momentem obrotowym, aby uniknąć uszkodzenia ramy panelu lub samego optymalizatora. Zaletą tego rozwiązania jest minimalizacja dodatkowych elementów montażowych i estetyka – optymalizator jest dyskretnie ukryty za panelem. Minusem może być nieco trudniejszy dostęp w przypadku serwisu lub wymiany w przyszłości, choć nie jest to regułą. Przykładowo, optymalizatory SolarEdge często wykorzystują system zatrzaskowy, który pozwala na szybki montaż i demontaż bez użycia narzędzi.
Montaż do konstrukcji wsporczej jest preferowany w sytuacjach, gdy rama panelu nie jest odpowiednia do bezpośredniego montażu, lub gdy instalator chce zapewnić lepszy dostęp do optymalizatorów. W tym przypadku optymalizatory mocuje się za pomocą śrub lub obejm do profili konstrukcji. Ważne jest, aby wybrać odpowiednie elementy montażowe, odporne na korozję i warunki atmosferyczne. Przy montażu do konstrukcji warto zadbać o odpowiednie ułożenie kabli, aby były one chronione przed uszkodzeniami mechanicznymi i naprężeniami. Można wykorzystać opaski kablowe, rurki ochronne lub kanały kablowe, aby estetycznie i bezpiecznie poprowadzić przewody. Zaletą montażu do konstrukcji jest lepszy dostęp serwisowy i potencjalnie lepsze chłodzenie optymalizatorów, co może mieć znaczenie w gorącym klimacie. Minusem jest konieczność użycia dodatkowych elementów montażowych i nieco bardziej skomplikowany proces instalacji. Niektórzy producenci optymalizatorów oferują specjalne uchwyty montażowe, dedykowane do konkretnych typów konstrukcji, co ułatwia i przyspiesza instalację.
Niezależnie od wybranej metody montażu, kluczowe jest solidne i bezpieczne zamocowanie optymalizatora. Urządzenie nie może się przesuwać, wibrować ani być narażone na nadmierne naprężenia mechaniczne. Upewnij się, że optymalizator jest zamocowany w orientacji zgodnej z zaleceniami producenta – zazwyczaj pozycja pionowa sprzyja lepszemu chłodzeniu. Sprawdź, czy optymalizator nie blokuje otworów wentylacyjnych panelu PV (jeśli takie istnieją) i czy nie utrudnia naturalnej wentylacji. Prawidłowy montaż mechaniczny to fundament dla dalszych etapów instalacji i długotrwałej, bezawaryjnej pracy systemu. To jak solidne fundamenty domu – jeśli są wadliwe, cała konstrukcja może być zagrożona.
Elektryczne Podłączenie Optymalizatorów do Modułów PV
Po mechanicznym zamocowaniu optymalizatorów, kolejnym, kluczowym krokiem jest elektryczne podłączenie optymalizatorów do modułów PV. To etap, gdzie precyzja i wiedza z zakresu elektrotechniki grają pierwsze skrzypce. Błędy w połączeniach elektrycznych to najczęstsza przyczyna problemów w instalacjach fotowoltaicznych – od spadku wydajności, przez uszkodzenie komponentów, po ryzyko pożaru. Dlatego, zanim przystąpisz do podłączania kabli, upewnij się, że masz odpowiednią wiedzę i narzędzia, a przede wszystkim – wyłącz zasilanie po stronie AC i DC systemu fotowoltaicznego. Bezpieczeństwo jest zawsze najważniejsze! To jak praca przy otwartym sercu – każdy ruch musi być przemyślany i wykonany z największą starannością.
Standardowo, optymalizatory mocy podłącza się szeregowo między panelem fotowoltaicznym a stringiem kablowym prowadzącym do inwertera. Każdy optymalizator posiada wejście (input) i wyjście (output). Wejście optymalizatora podłączamy do złączek wyjściowych panelu PV (zazwyczaj złącza MC4 – męskie i żeńskie). Wyjście optymalizatora podłączamy do stringu kablowego, który wcześniej był podłączony bezpośrednio do panelu. Proces ten powtarzamy dla każdego panelu w stringu, który ma być wyposażony w optymalizator. Kluczowe jest zachowanie prawidłowej polaryzacji – plus do plusa, minus do minusa. Złącza MC4 są zazwyczaj kolorami oznaczone (czerwony – plus, czarny – minus) i posiadają system zapobiegający odwrotnemu podłączeniu, ale zawsze warto to dodatkowo sprawdzić. Pomylenie polaryzacji to szybka droga do uszkodzenia elektroniki optymalizatora lub panelu. To jak podłączenie akumulatora samochodowego na odwrót – efekty mogą być dramatyczne.
Podczas podłączania złączek MC4, upewnij się, że są one dokładnie i mocno złączone. Powinno być słyszalne charakterystyczne „kliknięcie”. Następnie, dokręć złączki ręcznie, a na koniec – użyj klucza dynamometrycznego, aby dokręcić je z odpowiednim momentem obrotowym (zgodnie z instrukcją producenta złączek, zazwyczaj 2-3 Nm). Poprawne dokręcenie złączek MC4 to absolutna konieczność – zapobiega to przedostawaniu się wilgoci, kurzu i zapewnia pewny kontakt elektryczny. Niedokręcone złącze to potencjalne źródło problemów – od wzrostu rezystancji i strat energii, po iskrzenie, przegrzewanie i ryzyko pożaru. Nie oszczędzaj czasu na dokładnym dokręcaniu złączek – to inwestycja w bezpieczeństwo i wydajność instalacji. Pamiętaj, że złącza MC4 są elementem narażonym na działanie warunków atmosferycznych – słońca, deszczu, śniegu, wiatru, wahania temperatur. Solidne połączenie to gwarancja długotrwałej i bezawaryjnej pracy.
Po podłączeniu wszystkich optymalizatorów w stringu, sprawdź poprawność połączeń za pomocą multimetru. Zmierz napięcie na wejściu i wyjściu każdego optymalizatora – powinno być zbliżone do napięcia otwartego obwodu panelu (Voc) w warunkach braku obciążenia. Sprawdź ciągłość obwodu – upewnij się, że nie ma przerw w połączeniach szeregowych. Dokonaj pomiaru prądu zwarcia (Isc) stringu za pomocą miernika cęgowego DC – wartość powinna być zbliżona do sumy prądów zwarcia paneli w stringu (przy założeniu podobnych warunków nasłonecznienia). Pomiary to Twoja „checklista bezpieczeństwa” – potwierdzenie, że wszystko zostało podłączone prawidłowo i instalacja jest gotowa do uruchomienia. Wykonanie dokładnych pomiarów to jak kontrola jakości w fabryce – eliminujesz błędy na wczesnym etapie i unikasz kosztownych napraw w przyszłości.
Pamiętaj o zarządzaniu kablami. Ułóż kable estetycznie i bezpiecznie, unikając ostrych zagięć i naprężeń. Użyj opasek kablowych, uchwytów lub kanałów kablowych, aby przymocować kable do konstrukcji i paneli. Zabezpiecz kable przed przetarciem o ostre krawędzie konstrukcji. Dobre zarządzanie kablami to nie tylko kwestia estetyki – to również bezpieczeństwo i trwałość instalacji. Uporządkowane kable są mniej narażone na uszkodzenia mechaniczne i łatwiejsze w diagnostyce i serwisie. Wyobraź sobie plątaninę kabli – w razie awarii, znalezienie i naprawa problemu staje się koszmarem.
Na koniec, po zakończeniu elektrycznego podłączania optymalizatorów, dokonaj wizualnej inspekcji wszystkich połączeń. Sprawdź, czy złączki są dobrze dokręcone, kable poprawnie ułożone i zabezpieczone, a optymalizatory solidnie zamocowane. Upewnij się, że nie ma żadnych luźnych kabli, ostrych krawędzi, czy innych potencjalnych zagrożeń. Ostatni rzut oka to jak podpisanie się pod dziełem – potwierdzenie, że wykonałeś pracę z należytą starannością i dbałością o szczegóły.
Konfiguracja i Uruchomienie Systemu Optymalizacji Mocy: Integracja z Inwerterem
Po pomyślnym przejściu przez etap fizycznego montażu i podłączenia elektrycznego, finalnym akordem staje się konfiguracja i uruchomienie systemu optymalizacji mocy w integracji z inwerterem. Ten krok to moment kulminacyjny, w którym wszystkie elementy zaczynają grać w orkiestrze fotowoltaicznej, harmonijnie współpracując dla maksymalizacji produkcji energii. To jak dyrygent, który ustawia instrumenty i nadaje ton całemu zespołowi – Ty, jako instalator, konfigurujesz system, aby pracował synchronicznie i efektywnie. Pamiętaj, dobrze zestrojona orkiestra gra pięknie i czysto – podobnie, poprawnie skonfigurowana instalacja fotowoltaiczna pracuje wydajnie i niezawodnie przez lata.
Komunikacja Optymalizatorów z Inwerterem: Parowanie i Adresowanie
Kluczowym elementem konfiguracji systemu z optymalizatorami jest ustanowienie komunikacji pomiędzy optymalizatorami a inwerterem. To fundament, na którym opiera się cały system monitorowania i optymalizacji pracy paneli. Bez komunikacji, optymalizatory są tylko pasywnymi elementami, a ich potencjał pozostaje niewykorzystany. Wyobraź sobie inteligentny dom, w którym urządzenia nie są połączone z siecią – każde działa osobno, bez synchronizacji i optymalizacji. Podobnie, system fotowoltaiczny bez komunikacji to zbiór elementów, a nie zintegrowana, inteligentna całość.
Proces parowania (pairing) lub adresowania optymalizatorów z inwerterem różni się w zależności od producenta i modelu urządzeń, ale ogólna zasada pozostaje podobna. Zazwyczaj, proces inicjowany jest z poziomu inwertera, poprzez menu konfiguracyjne lub dedykowaną aplikację mobilną/webową. Inwerter wysyła sygnał, na który optymalizatory odpowiadają, zgłaszając swoją obecność w systemie. W niektórych systemach, parowanie jest automatyczne – po uruchomieniu inwertera, automatycznie wykrywa i paruje się z optymalizatorami. W innych, konieczne jest ręczne adresowanie każdego optymalizatora, zazwyczaj poprzez skanowanie kodów QR lub wprowadzanie numerów seryjnych z naklejek umieszczonych na optymalizatorach. Metoda ręczna jest bardziej czasochłonna, ale zapewnia większą kontrolę nad procesem parowania, szczególnie w dużych instalacjach. Automatyczne parowanie jest szybsze i wygodniejsze, ale może być mniej precyzyjne w skomplikowanych konfiguracjach. Przykładowo, systemy SolarEdge wykorzystują automatyczne parowanie, natomiast Tigo – często wymagają ręcznego skanowania kodów QR.
Podczas procesu parowania, ważne jest ścisłe przestrzeganie instrukcji producenta. Każdy system ma swoje specyficzne procedury i niuanse, które mogą mieć wpływ na powodzenie procesu. Upewnij się, że inwerter i optymalizatory są w zasięgu komunikacji – zazwyczaj komunikacja odbywa się po kablach DC (Power Line Communication – PLC) lub bezprzewodowo (ZigBee, WiFi). W przypadku PLC, nie ma dodatkowych wymagań dotyczących zasięgu, komunikacja odbywa się po istniejącym okablowaniu. W przypadku komunikacji bezprzewodowej, odległość między inwerterem a najdalszym optymalizatorem może być ograniczona. Sprawdź w specyfikacji producenta maksymalny zasięg komunikacji bezprzewodowej i upewnij się, że Twoja instalacja mieści się w tych limitach. Jeśli instalacja jest rozległa, konieczne może być zastosowanie repeaterów sygnału lub wzmacniaczy, aby zapewnić niezawodną komunikację. Zakłócenia elektromagnetyczne mogą również wpływać na komunikację bezprzewodową – unikaj prowadzenia kabli komunikacyjnych w pobliżu silnych źródeł zakłóceń (np. transformatorów, silników elektrycznych).
Po pomyślnym sparowaniu optymalizatorów z inwerterem, w systemie monitoringu (aplikacji mobilnej lub platformie webowej) powinieneś zobaczyć listę zarejestrowanych optymalizatorów, przypisanych do poszczególnych paneli. Sprawdź, czy wszystkie optymalizatory zostały wykryte i poprawnie przypisane. Jeśli brakuje jakiegoś optymalizatora na liście, sprawdź połączenia, zasięg komunikacji i powtórz proces parowania. System monitoringu to Twoje „centrum dowodzenia” – z poziomu aplikacji lub platformy webowej możesz śledzić wydajność każdego panelu, monitorować napięcia, prądy, moc, temperaturę, diagnozować ewentualne problemy i zdalnie zarządzać systemem. To jak kokpit nowoczesnego samolotu – pilot ma dostęp do wszystkich kluczowych parametrów lotu i może reagować na bieżąco na wszelkie zmiany.
W zaawansowanych systemach optymalizacji mocy, istnieje możliwość grupowania optymalizatorów w stringi i definiowania układu paneli na dachu (layout) w systemie monitoringu. Funkcja grupowania ułatwia zarządzanie dużymi instalacjami – możesz monitorować wydajność całych stringów, zamiast każdego panelu osobno. Definiowanie layoutu dachu w systemie monitoringu pozwala na wizualizację rozmieszczenia paneli i optymalizatorów na dachu – co ułatwia lokalizację ewentualnych problemów i planowanie prac serwisowych. Wyobraź sobie mapę dachu z zaznaczonymi panelami i ich aktualną wydajnością – w mgnieniu oka widzisz, gdzie występują ewentualne zacienienia lub problemy. Niektórzy producenci oferują nawet funkcję zdalnej diagnostyki i konfiguracji optymalizatorów, co pozwala na rozwiązywanie problemów bez konieczności fizycznego dostępu do instalacji. To jak zdalna pomoc techniczna – specjalista może zdiagnozować problem i często rozwiązać go online, oszczędzając czas i koszty dojazdu.
Konfiguracja Parametrów Pracy i Testowanie Systemu
Po ustanowieniu komunikacji i konfiguracji topologii systemu, nadszedł czas na konfigurację parametrów pracy i testowanie systemu optymalizacji mocy. Ten etap to weryfikacja, czy system działa zgodnie z oczekiwaniami, czy optymalizatory prawidłowo regulują moc paneli i czy cała instalacja generuje maksymalną możliwą energię. To jak strojenie instrumentów przed koncertem – każdy element musi być perfekcyjnie dostrojony, aby orkiestra zagrała symfonię mocy i efektywności.
W menu konfiguracyjnym inwertera lub w aplikacji monitorującej, znajdziesz szereg ustawień związanych z optymalizacją mocy. Najczęściej spotykane parametry to tryb pracy optymalizatorów (np. standardowy, zaawansowany, inteligentny), progi alarmowe (np. dla napięcia, prądu, temperatury), ustawienia komunikacji (np. adres IP, protokół komunikacyjny), ustawienia bezpieczeństwa (np. Rapid Shutdown). Dokładne nazwy i zakres dostępnych ustawień zależą od producenta i modelu inwertera oraz optymalizatorów. Przed przystąpieniem do konfiguracji, zapoznaj się dokładnie z instrukcją obsługi i zaleceniami producenta. Nie eksperymentuj na ślepo – nieprawidłowe ustawienia mogą obniżyć wydajność systemu lub nawet spowodować jego uszkodzenie. To jak programowanie robota – zły kod może sprawić, że robot zamiast pomagać, zacznie przeszkadzać.
W trybie pracy optymalizatorów, zazwyczaj masz do wyboru kilka opcji. Tryb standardowy (by-pass) – optymalizatory działają w trybie pasywnym, przepuszczając prąd z paneli do inwertera, bez aktywnej optymalizacji. Ten tryb może być przydatny w sytuacjach, gdy warunki nasłonecznienia są idealne i optymalizacja nie jest potrzebna, lub w celach diagnostycznych. Tryb zaawansowany (optymalizacja) – optymalizatory aktywnie poszukują punktu mocy maksymalnej (MPPT) dla każdego panelu, regulując napięcie i prąd, aby zmaksymalizować produkcję energii, szczególnie w warunkach częściowego zacienienia lub nierównomiernego nasłonecznienia. Tryb inteligentny (hybrydowy) – optymalizatory automatycznie dostosowują tryb pracy w zależności od warunków nasłonecznienia i potrzeb systemu. W idealnych warunkach pracują w trybie pasywnym, oszczędzając energię i wydłużając żywotność, w warunkach zacienienia – przełączają się na tryb aktywnej optymalizacji. Wybór trybu pracy zależy od specyfiki instalacji, lokalnych warunków nasłonecznienia i preferencji użytkownika. W większości przypadków, tryb zaawansowany lub inteligentny jest zalecany, aby w pełni wykorzystać potencjał optymalizatorów.
Po skonfigurowaniu parametrów pracy, przeprowadź testy systemu, aby zweryfikować jego prawidłowe działanie. Obserwuj parametry pracy systemu w systemie monitoringu – napięcia, prądy, moc, wydajność poszczególnych paneli i całego stringu. Sprawdź, czy optymalizatory aktywnie pracują – w systemie monitoringu powinny być widoczne dane dotyczące pracy każdego optymalizatora. Zasymuluj warunki zacienienia – np. zakrywając część paneli kartonem lub folią. Obserwuj, jak system reaguje na zacienienie – czy wydajność zacienionych paneli spada, a wydajność pozostałych paneli pozostaje na wysokim poziomie. W systemie bez optymalizatorów, zacienienie jednego panelu znacząco obniżyłoby wydajność całego stringu. Dzięki optymalizatorom, efekt ten powinien być minimalny. Porównaj wydajność systemu z optymalizatorami i bez optymalizatorów (jeśli masz taką możliwość) w różnych warunkach nasłonecznienia. Dane z testów to Twój „dowód skuteczności” – potwierdzenie, że system optymalizacji mocy działa prawidłowo i przynosi realne korzyści. To jak jazda testowa samochodem – sprawdzasz, czy wszystko działa, jak powinno i czy samochód spełnia Twoje oczekiwania.
Nie zapomnij o funkcjach bezpieczeństwa, takich jak Rapid Shutdown. Przetestuj działanie systemu szybkiego wyłączania – upewnij się, że po aktywacji funkcji, napięcie po stronie DC instalacji spada do bezpiecznego poziomu w określonym czasie (zgodnie z normami bezpieczeństwa). Funkcja Rapid Shutdown jest szczególnie ważna dla bezpieczeństwa strażaków i ekip ratowniczych w przypadku pożaru lub awarii. Regularne testowanie funkcji bezpieczeństwa to jak przegląd gaśnic w budynku – upewniasz się, że w razie potrzeby zadziałają prawidłowo i ochronią życie i mienie.
Na koniec, po przeprowadzeniu wszystkich testów i weryfikacji, zarejestruj system w systemie monitoringu producenta i przekaż dokumentację instalacji użytkownikowi końcowemu. Dokumentacja powinna zawierać schemat instalacji, instrukcje obsługi inwertera i optymalizatorów, wyniki testów, certyfikaty i gwarancje. Kompletna i rzetelna dokumentacja to Twój „paszport instalacji” – potwierdzenie jakości wykonanej pracy i podstawa do ewentualnych roszczeń gwarancyjnych. To jak archiwum projektu – wszystkie kluczowe informacje zebrane w jednym miejscu, dostępne na przyszłość.