Dlaczego palą się panele fotowoltaiczne w 2025 roku? Główne przyczyny pożarów instalacji PV
Inwestycja w energię słoneczną to krok w przyszłość, symbol nowoczesności i świadomości ekologicznej, jednak pod szlachetnym słońcem czasem czai się mniej poetycki problem. Z każdym rokiem rośnie liczba instalacji, a wraz z nią pojawiają się pytania, na które warto znać odpowiedź – na przykład Dlaczego palą się panele fotowoltaiczne? Ta kwestia, często obrosła w mity, sprowadza się do kilku kluczowych przyczyn, a krótko mówiąc, pożary instalacji fotowoltaicznych powstają głównie w wyniku problemów technicznych i ludzkich błędów. Rozprawmy się z obawami i zajrzyjmy pod powierzchnię dachu.
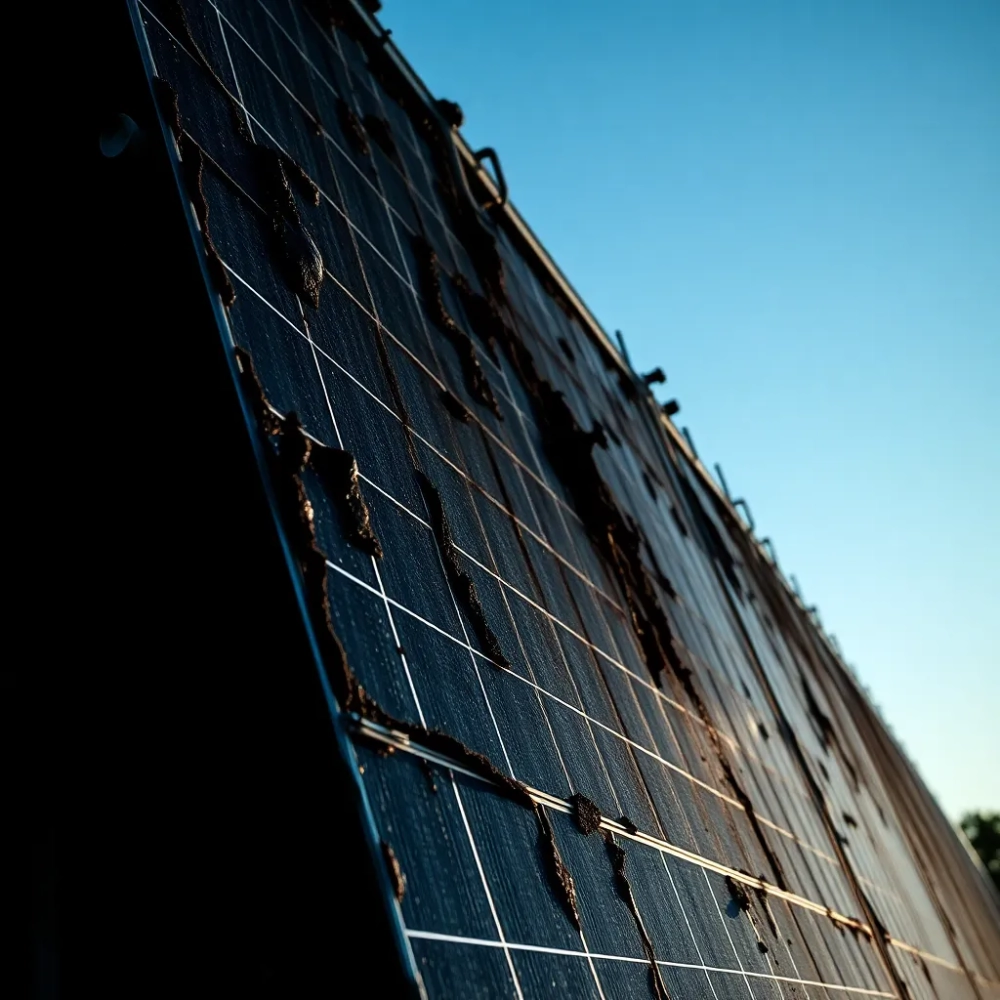
Rok | Szacowana liczba instalacji PV (Polska) | Zgłoszenia pożarów z udziałem instalacji PV | Pożary w obiektach mieszkalnych z PV | Szacowany odsetek pożarów PV vs. ogół pożarów obiektów mieszkalnych (z PV) |
2018 | ~150 000 | ~30 | ~20 | ~0.01% |
2019 | ~250 000 | ~45 | ~30 | ~0.012% |
2020 | ~500 000 | ~100 | ~70 | ~0.014% |
2021 | ~850 000 | ~170 | ~120 | ~0.014% |
2022 | ~1 200 000 | ~230 | ~160 | ~0.013% |
2023 | ~1 450 000 | ~280 | ~200 | ~0.014% |
Łuk elektryczny DC – najgroźniejszy typ zwarcia w instalacjach PV
Kiedy mówimy o pożarach instalacji fotowoltaicznych, często na pierwszy plan wysuwa się pojęcie łuku elektrycznego prądu stałego (DC). To zjawisko jest postrzegane jako jedno z najpoważniejszych zagrożeń i ma swoje specyficzne, diabelskie wręcz cechy, które odróżniają je od zwarć w instalacjach prądu przemiennego (AC), znanych nam z domowych gniazdek. Wyobraźmy sobie instalację PV jako system, gdzie na dachu mamy kilkanaście czy kilkadziesiąt modułów połączonych szeregowo, generujących wysokie napięcie DC, często w przedziale od 400 V do nawet 1000 V czy więcej w zależności od rozmiaru i konfiguracji.
Co odróżnia prąd stały od przemiennego? Prąd AC w europejskich sieciach zmienia kierunek przepływu 50 razy na sekundę, co oznacza, że przechodzi przez zero. Jeśli powstanie łuk, to cykliczne zerowanie napięcia i prądu daje mu szansę na samoistne zgaszenie przy każdym przejściu przez punkt zero. Prąd DC płynie zawsze w jednym kierunku z mniej więcej stałym napięciem (gdy słońce świeci), nie ma więc tego naturalnego "okienka" do zgaszenia. Kiedy już raz powstanie łuk DC, jest on znacznie trudniejszy do przerwania – potrafi utrzymać się stabilnie, uwalniając ogromne ilości energii cieplnej. To jak mini spawarka, która bezlitośnie topi i zapala materiały, z którymi ma kontakt, takie jak plastikowa izolacja kabli, obudowy modułów czy materiały dachu.
Łuk DC powstaje najczęściej w miejscach, gdzie dochodzi do przerwania ciągłości obwodu lub degradacji izolacji, przy jednoczesnym występowaniu wysokiego napięcia i prądu. Typowe punkty krytyczne to przede wszystkim połączenia w skrzynkach przyłączeniowych modułów (tzw. junction boxy), połączenia pomiędzy modułami (najczęściej za pomocą złącz typu MC4, choć rynek oferuje różne warianty), połączenia w rozdzielnicy DC przed inwerterem oraz wszelkie miejsca, gdzie okablowanie może ulec uszkodzeniu mechanicznemu (przy montażu, przez zwierzęta) lub degradacji pod wpływem czynników atmosferycznych (słońce, temperatura). Luźne lub źle zaciśnięte złącza, uszkodzona izolacja, korozja styków – to idealne scenariusze dla narodzin destrukcyjnego łuku.
Energia uwalniana przez łuk DC może być gigantyczna. Wyobraźmy sobie prąd o natężeniu kilku amperów i napięciu 600V, który tworzy łuk przez kilka sekund lub minut. To oznacza uwalnianie energii rzędu kilkuset, a nawet tysięcy watów, skoncentrowanej na niewielkiej przestrzeni. Temperatura łuku może sięgać kilku tysięcy stopni Celsjusza. Panele, kable i elementy konstrukcyjne, zbudowane w dużej mierze z materiałów palnych (polimery, tworzywa sztuczne), stają się paliwem dla takiego łuku, który błyskawicznie rozprzestrzenia ogień.
Producenci i regulatorzy zdają sobie sprawę z tego zagrożenia, dlatego standardy bezpieczeństwa dla instalacji PV ewoluują, wprowadzając technologie mające na celu wykrywanie i jak najszybsze przerywanie łuku DC. Przykładem są zabezpieczenia typu AFCI (Arc Fault Circuit Interrupter), które monitorują sygnaturę elektryczną prądu w obwodzie DC i potrafią rozpoznać charakterystyczny szum i zakłócenia generowane przez łuk elektryczny, aby błyskawicznie rozłączyć obwód. Wiele nowoczesnych inwerterów ma wbudowaną taką funkcjonalność. Dodatkowo, systemy szybkiego wyłączania (Rapid Shutdown) na poziomie modułu lub grupy modułów pozwalają strażakom lub serwisantom na bezpieczne obniżenie napięcia DC na dachu, minimalizując ryzyko porażenia lub powstania łuku podczas akcji gaśniczej czy serwisowej. Nie jest to cudowny lek na wszystko, ale znacząco zwiększa bezpieczeństwo. Nie można przecież oczekiwać, że strażak, wchodząc na dach, będzie się zastanawiał, czy instalacja ma napięcie 1000V DC, czy jest bezpiecznie rozłączona. Potrzebują prostego, szybkiego sposobu na neutralizację zagrożenia elektrycznego.
Historycznie, niedostateczna wiedza na temat specyfiki prądu stałego wysokiego napięcia w kontekście pożarowym przyczyniła się do rozwoju sytuacji, w której łuk DC stał się "ciemną stroną mocy" fotowoltaiki. Starsze instalacje, projektowane i montowane przed upowszechnieniem technologii AFCI czy Rapid Shutdown, są potencjalnie bardziej narażone na to zjawisko. Dlatego też regularne przeglądy i modernizacje mogą być kluczowe. Współczesne komponenty i standardy kładą coraz większy nacisk na minimalizowanie ryzyka łuku – od ulepszonych materiałów izolacyjnych, przez złącza o wyższej trwałości i lepszym kontakcie, po zaawansowaną elektronikę monitorującą instalację na bieżąco. Niestety, żaden system nie jest absolutnie niezawodny, a czujność i prawidłowa eksploatacja pozostają fundamentalne. Skala zagrożenia, choć statystycznie mała, jest na tyle poważna w przypadku wystąpienia, że nie wolno jej lekceważyć – to jest zagrożenie związane z pożarem fotowoltaiki wymagające szczególnej uwagi.
Znaczenie jakości paneli, inwerterów i okablowania w bezpieczeństwie instalacji
Prawda stara jak świat: jakość kosztuje. W przypadku instalacji fotowoltaicznej, która ma nam służyć bezawaryjnie przez 25 lat lub dłużej, ta maksyma nabiera szczególnego znaczenia, zwłaszcza w kontekście bezpieczeństwa pożarowego. Każdy element systemu – od paneli krzepiących się na słońcu na dachu, przez falownik (inwerter) przetwarzający prąd stały na zmienny, aż po setki metrów kabli i dziesiątki złączy – musi spełniać rygorystyczne normy i charakteryzować się wysoką jakością wykonania. Jeśli jeden element zawiedzie, może to uruchomić kaskadę zdarzeń prowadzącą do poważnych problemów, w tym ryzyku powstania pożaru.
Zacznijmy od paneli. Moduły fotowoltaiczne to nie tylko krzemowe ogniwa. To złożone "sandwich", w którym ogniwa są zalaminowane między warstwami folii EVA, chronione przez hartowane szkło od przodu i warstwę backsheetu od tyłu, całość zamknięta w ramie z aluminium i połączona z puszką przyłączeniową (junction box) na tylnej stronie. Niska jakość może objawiać się na wiele sposobów: użycie słabych materiałów do laminacji prowadzące do delaminacji i przenikania wilgoci, co skutkuje korozją i uszkodzeniem ogniw; zastosowanie tandetnego szkła podatnego na pęknięcia pod wpływem naprężeń termicznych lub obciążeń; czy wreszcie felerna puszka przyłączeniowa ze słabymi diodami bypass (które mogą przegrzewać się i zapalać) lub niskiej jakości złączami i okablowaniem wychodzącym z puszki. Widzieliśmy przypadki, gdzie problemem były przegrzewające się diody bypass, które po prostu zaczęły się palić wewnątrz puszki przyklejonej do panelu. Innym razem to problem z samą laminacją, gdzie wilgoć i brud tworzą ścieżki upływu prądu, prowadząc do gorących punktów (hot spotów) na powierzchni panelu, które mogą doprowadzić do zapłonu materiałów modułu.
Inwerter, serce instalacji, również musi być produktem wysokiej klasy. Pracuje on w trudnych warunkach – często na zewnątrz, narażony na zmiany temperatury, wilgoć i pył, przetwarzając znaczące moce. Wadliwe komponenty elektroniczne, niewystarczające chłodzenie, błędy w oprogramowaniu czy słabe zabezpieczenia przepięciowe lub zwarciowe mogą prowadzić do przegrzewania, iskrzenia wewnątrz obudowy lub awarii, która zainicjuje pożar. Szczególnie newralgiczne są elementy mocy i systemy rozłączania, które muszą być niezawodne. Inwertery posiadające odpowiednie certyfikaty bezpieczeństwa (nie tylko te elektryczne, ale i dotyczące bezpieczeństwa pożarowego, jak np. możliwość szybkiego wyłączania po stronie DC) stanowią mniejsze zagrożenie pożarowe związane z ogniwami fotowoltaicznymi i całym systemem. Nie oszczędza się na hamulcach w samochodzie i podobnie nie powinno się oszczędzać na kluczowym urządzeniu elektrycznym w instalacji PV.
Okablowanie i złącza – to często niedoceniane, ale niezwykle ważne elementy, które są źródłem wielu problemów. Kable DC w instalacjach PV pracują pod wysokim napięciem i są narażone na ekstremalne warunki: wysokie i niskie temperatury, promieniowanie UV, deszcz, śnieg, lód. Kable przeznaczone do fotowoltaiki muszą spełniać bardzo wysokie wymagania dotyczące izolacji, odporności mechanicznej i trwałości. Zastosowanie zwykłych kabli elektroenergetycznych, nieprzystosowanych do specyficznych warunków instalacji PV, to prosta droga do katastrofy. Izolacja takiego kabla szybko degraduje pod wpływem UV i temperatury, pęka, odsłaniając przewody, co może prowadzić do zwarć doziemnych, międzybiegunowych, a w konsekwencji do powstania łuku. Złącza MC4, choć powszechnie stosowane, są elementem, który wymaga największej uwagi podczas montażu i wyboru producenta. Słabej jakości złącza, wykonane z materiałów, które tracą sprężystość, korodują lub są podatne na pękanie, to częsta przyczyna luźnych połączeń, a te, jak już wiemy, są wylęgarnią łuków DC. Wystarczy spojrzeć na przekrój markowego złącza i porównać go z najtańszym odpowiednikiem – różnica w grubości plastiku, jakości styków i szczelności jest często gołym okiem widoczna. W końcu, niech pan "Januszex" nie opowiada, że "kabel to kabel" – w PV tak to nie działa. To właśnie te drobne, pozornie tanie elementy, potrafią doprowadzić do gigantycznych szkód, a inwestycja w kable i złącza najwyższej klasy od renomowanych producentów, posiadających odpowiednie certyfikaty (jak np. Tüv Rheinland, zgodność z normą PN-EN 50618), to inwestycja bezpośrednio w bezpieczeństwo i długowieczność instalacji. Ich koszt stanowi relatywnie niewielką część całej inwestycji (powiedzmy, kilka procent całkowitej ceny instalacji rzędu 30-50 tysięcy złotych dla domu jednorodzinnego), a oszczędności w tej sferze są fałszywą oszczędnością, która może słono kosztować. Odpowiedni dobór przekrojów kabli również jest kluczowy, aby uniknąć przegrzewania pod obciążeniem. Podsumowując, kupowanie najtańszych komponentów z niepewnego źródła, bez wymaganych certyfikatów, jest jak gra w rosyjską ruletkę z ogniem – prędzej czy później ktoś pociągnie za spust. Inwestując w jakość, minimalizujemy wiele potencjalnych źródeł awarii, w tym tych prowadzących do pożaru.
Wpływ błędów montażowych na ryzyko pożaru instalacji fotowoltaicznej
Nawet najlepsze, najdroższe komponenty, z certyfikatami godnymi alpejskiego złota, nie zagwarantują bezpieczeństwa, jeśli zostaną zamontowane przez osoby niekompetentne lub lekceważące zasady sztuki budowlanej i elektrycznej. Okazuje się, że spora część pożarów instalacji PV ma swoje źródło w błędach popełnionych właśnie na etapie instalacji. Człowiek, ze swoją kreatywnością i... czasami, niestety, ignorancją, potrafi pokrzyżować szyki nawet najnowocześniejszym technologiom. Mówi się, że ponad 50% problemów z instalacjami PV (nie tylko pożarów) wynika z błędów wykonawczych. Brzmi druzgocąco, ale ma niestety solidne podstawy.
Najczęstsze grzechy montażowe to przede wszystkim problemy ze wspomnianymi wcześniej złączami. Nieprawidłowe zarobienie złączy, użycie narzędzi, które nie są dedykowane do danego typu konektora (np. zaciskanie obcęgami zamiast specjalną praską do MC4), mieszanie złączy różnych producentów (co może prowadzić do niedopasowania styków i spadków rezystancji połączenia) – wszystko to skutkuje zwiększoną rezystancją, która przy przepływie prądu zamienia się w ciepło. Jeśli ciepła jest dużo, izolacja i plastik wokół zaczynają się topić, a to idealny przepis na powstanie łuku DC. Często widzi się kable w puszkach przyłączeniowych paneli, które po kilku latach wyglądają jak spalone zapałki – to właśnie efekt wadliwego połączenia.
Kolejny arcyważny aspekt to zarządzanie okablowaniem (cable management). Kable DC prowadzone po dachu i pod panelami są narażone na czynniki środowiskowe i mechaniczne. Jeśli kable nie są odpowiednio zabezpieczone przed promieniowaniem UV (np. w korytkach czy rurach instalacyjnych odpornych na UV), ich izolacja szybciej ulegnie degradacji. Jeśli są niedbale ułożone i zwisają luźno, mogą ocierać się o ostre krawędzie konstrukcji montażowej, dachówek czy blachy, co z czasem przetrze izolację. Jeśli zostaną przygniecione podczas montażu paneli lub wciśnięte w zbyt wąskie przestrzenie, uszkodzenie izolacji jest niemal pewne. Złamany kabel, nawet częściowo, staje się punktem gorącym i potencjalnym źródłem łuku. Wystarczy jedno niewłaściwie założone spoiwo kablowe czy przypadkowe przytrzaśnięcie kabla, aby zasiano ziarno problemu, które wykiełkuje za rok czy dwa.
Inne błędy montażowe obejmują: nieprawidłowe podłączenie inwertera, niezachowanie odpowiednich odległości między elementami przewodzącymi prąd a konstrukcją dachu czy innymi materiałami palnymi, brak uziemienia lub nieprawidłowe uziemienie konstrukcji i paneli (co jest kluczowe dla bezpieczeństwa i ochrony przed przepięciami atmosferycznymi, które też mogą być przyczyną pożaru), a także nieprofesjonalne przejścia przez dach (nieuszczelnione, uszkadzające hydroizolację i potencjalnie kable). Wyobraźcie sobie instalatora, który z pośpiechu czy niewiedzy nie uszczelnia odpowiednio przejścia kabla przez dach – do środka może wciekać woda, która w kontakcie z prądem i zanieczyszczeniami tworzy ścieżki upływu, prowadzące do zwarć. Taka sytuacja nie tylko grozi pożarem, ale i zniszczeniem samego dachu czy stropu.
Studium przypadku z życia: Pewna instalacja na domu jednorodzinnym po trzech latach zaczęła zgłaszać alarmy błędu izolacji. Podczas przeglądu okazało się, że kable DC puszczone bez peszla bezpośrednio po metalowym dachu ocierały się o kant blachy. Izolacja w dwóch miejscach została całkowicie przetarta. Jeszcze trochę, a mogłoby dojść do zwarcia doziemnego lub międzyżyłowego. Na szczęście wykryto to w porę. Koszt naprawy? Wymiana kabli, nowe złącza, odpowiednie peszle i zabezpieczenia. Ale strach i świadomość, jak blisko było od pożaru, pozostały. To klasyczny przykład ryzyka wystąpienia pożaru w moim domu z powodu błędu montażowego. Podkreślmy raz jeszcze: brak fachowości instalatora to jedno z największych zagrożeń. Instalatorzy powinni posiadać odpowiednie kwalifikacje, doświadczenie i przede wszystkim stosować się do instrukcji producentów oraz obowiązujących norm. Czy ktoś powierzyłby montaż instalacji gazowej przypadkowej osobie "bo taniej"? No właśnie. Z fotowoltaiką powinno być podobnie, bo choć nie ma tu wybuchów gazu, to zagrożenia elektryczne są realne i poważne.
Zapobieganie pożarom: Rola właściwego projektu, montażu i regularnej konserwacji
Skoro wiemy już, skąd bierze się licho, czyli Dlaczego palą się panele fotowoltaiczne w tych nielicznych, ale poważnych przypadkach, możemy przejść do sedna: jak skutecznie zapobiegać tym nieszczęściom. Odpowiedź jest w gruncie rzeczy prosta, choć jej realizacja wymaga dyscypliny i współpracy wszystkich zaangażowanych stron – od projektanta, przez instalatora, po samego inwestora. Kluczowe filary bezpieczeństwa to: przemyślany projekt, fachowy montaż i systematyczna konserwacja.
Właściwy projekt to fundament bezpiecznej instalacji. Dobry projektant weźmie pod uwagę specyfikę dachu (materiał pokrycia, kąt nachylenia, obciążenie), warunki zacienienia, optymalny dobór komponentów (panele, inwerter, optymalizatory/mikroinwertery jeśli potrzebne), odpowiednie zabezpieczenia elektryczne (rozłączniki DC i AC, zabezpieczenia przeciwprzepięciowe, bezpieczniki, system AFCI/Rapid Shutdown), a także zaplanuje bezpieczne prowadzenie okablowania. Zaprojektuje ścieżki kablowe w sposób minimalizujący ich długość i ekspozycję na uszkodzenia, przewidzi konieczność stosowania peszli, korytek, dławików. Pomyśli też o dostępie dla straży pożarnej, wskazując np. lokalizację rozłącznika DC w łatwo dostępnym miejscu. Dobry projekt nie tylko zmaksymalizuje produkcję energii, ale przede wszystkim zminimalizuje ryzyko pożaru.
Fachowy montaż jest drugim, absolutnie kluczowym elementem układanki. Nawet najlepszy projekt pozostanie tylko papierem, jeśli wykonawca podejdzie do zadania po macoszemu. Profesjonalni instalatorzy to osoby lub firmy posiadające odpowiednie uprawnienia (np. SEP, UDT do instalacji OZE), doświadczenie i przeszkolenie w zakresie montażu systemów PV i specyfiki pracy z wysokim napięciem DC. Taki instalator będzie wiedział, jak poprawnie zarobić złącza (używając odpowiedniej praski dynamometrycznej, która zaciska je z właściwą siłą), jak stosować wyłącznie kompatybilne złącza tego samego producenta (unikając "mieszańców", które kuszą niższą ceną), jak właściwie prowadzić i zabezpieczać kable (używając dedykowanych obejm, korytek odpornych na UV, przepustów dachowych zapewniających szczelność i ochronę kabli). Będzie dbał o każdy szczegół, wiedząc, że luźne połączenie czy uszkodzona izolacja to tykająca bomba.
Regularna konserwacja, choć często traktowana po macoszemu przez inwestorów, jest nieodzownym elementem utrzymania instalacji w bezpiecznym stanie. System PV, tak jak samochód czy piec grzewczy, wymaga okresowych przeglądów. Zaleca się, aby przeglądy wykonywać co najmniej raz na 1-2 lata. Co powinno być sprawdzone podczas takiego przeglądu? Wizualna inspekcja paneli pod kątem uszkodzeń mechanicznych (pęknięcia, delaminacja), stanu okablowania i złączy na dachu (czy nie są luźne, przetarte, czy izolacja nie jest zniszczona), sprawdzenie mocowania konstrukcji (czy nic się nie poluzowało, czy nie uszkodziło pokrycia dachowego). Niezbędne są też pomiary elektryczne – testy rezystancji izolacji przewodów i paneli, pomiary prądu i napięcia w stringach, a także pomiary termowizyjne, które pozwalają wykryć tzw. gorące punkty (hot spoty) – miejsca, gdzie generuje się nadmierne ciepło w wyniku wadliwego połączenia, uszkodzonego ogniwa, diody bypass, czy luźnego złącza. Wykrycie takiego punktu to wczesne ostrzeżenie przed potencjalną awarią lub pożarem. Pamiętajmy, że problem z luźnym złączem może rozwijać się przez długi czas, zanim stanie się na tyle poważny, by spowodować iskrzenie czy pożar. Regularny przegląd pozwala złapać problem w zarodku.
Koszty konserwacji? Typowy przegląd instalacji o mocy kilku kWp to koszt kilkuset złotych, rzędu 400-800 PLN w zależności od zakresu i regionu. W kontekście inwestycji za kilkadziesiąt tysięcy złotych, jest to niewielka kwota, która stanowi inwestycję w bezpieczeństwo i minimalizuje zagrożenia związane ze stosowaniem fotowoltaiki. Ignorowanie przeglądów to proszenie się o kłopoty. Ubezpieczenie instalacji PV jest oczywiście ważnym zabezpieczeniem finansowym w razie szkody, ale najlepszym "ubezpieczeniem" przed pożarem jest po prostu brak jego wystąpienia, co osiąga się przez profesjonalny projekt, montaż i regularną opiekę nad systemem. To jak przegląd u lekarza – profilaktyka jest zawsze lepsza i tańsza od leczenia zaawansowanej choroby. W końcu chodzi o bezpieczeństwo naszego domu i rodziny. To nie strachy na lachy, ale kwestia rozsądnego podejścia do technologii, która choć niesie wiele korzyści, jak każda instalacja elektryczna, wymaga traktowania z należytym respektem i profesjonalizmem na każdym etapie jej życia.